Situation
Waste Management is New Zealand’s leading provider of waste disposal services. Its purpose is to collect, transport, treat, recycle, recover and dispose off residential, commercial, and industrial waste. They operate facilities throughout the country dedicated to storing and processing all sorts of waste, from ordinary residential to liquid and hazardous waste.
In one of Waste Management facilities is a pond used for collecting water generated during the waste dewatering process. Recently, there has been an increase in waste inflow which raised the capacity requirement for the pond. This required for the pond to be modified to keep up with the inflow and improve the efficiency of its dewatering capacity.
Solution
The modification of Waste Management’s existing pond involved dividing it into to separate halves and adding an end extension. To do this, they considered a few options:
- Box-pour method
- Pre-poured tilt slab
- Interbloc Modular Wall System
Waste Management found the Interbloc Modular Wall System to be the ideal solution for this project. The box-pour method was prevented by the existing pond’s central wall height, while using pre-poured tilt slab proved too costly.
Using the Interbloc Modular Wall System allowed for the pond to be modified easily and cost-effectively. The system was quickly assembled despite the challenging environment of the pond. The installation process simply involved lifting the blocks into the pond using the lifting anchor and assembling them in the pond using a forklift. Ross, Waste Management’s Production Supervisor described the installation of the system an “easy, hassle free process”.
Benefits
Apart from the efficient installation process provided by the Interbloc Modular Wall System, Waste Management also obtained extra benefits for using Interbloc.
The modular quality of the blocks, along with its lifting anchor component, allowed for the structure to be safely installed. “Safety is held as our highest priority and value at Waste Management”, said Ross.
Furthermore, the modular quality of the blocks also provides Waste Management with the option to modify the pond in the future without any major construction.
Waste Management was also able to reduce their environmental footprint by using Interbloc’s Modular Wall system. Interbloc as a supporter of the Envirocon Product Stewardship Scheme provided them with environmentally sustainable products, which is line with Waste Management’s purpose of tackling New Zealand’s waste.
Pokeno’s uneven landscape makes retaining walls a must for many homeowners. Steve & Sopa are part of this group, searching for a solution for their newly built home.
After moving into their home a few months back, Steve and Sopa wanted to start improving their outdoor space. In Pokeno, rolling hills are often part of the landscape - meaning retaining walls are vital for creating usable space The main areas of focus were the driveway and the entertainment area that looks out towards the paddock.
Initially, timber was considered because they’re often seen as the go-to for retaining walls. With supply chain issues, higher installation costs, and many of their neighbors having timber retaining walls, Steve and Sopa searched for something different. To set themselves apart, they looked for a timber alternative.
After doing some research, they came across Stonebloc on Facebook. What stood out with Stonebloc was that it was “unique and something a bit different” (Steve and Sopa). They didn’t like seeing the fence posts of timber retaining walls, and Stonebloc “removed the obscured appearances the timber wall designs have”.
“We feel our home is one of our greatest assets. Stonebloc raises the looks and value of our home for us and our family’s future to enjoy”
How Stonebloc improved Steve & Sopa’s property:
- Created a retaining wall by their driveway, where fruit trees sit above
- Created a retaining wall that looks out at Pokeno farmland, doubling as an attractive entertainment area
Designing beautiful retaining walls with Stonebloc is simple from installation to maintenance - the perfect solution for homeowners. Better yet, it’s made for New Zealand meaning it fits in well with the country’s landscape.
Steve & Sopa recommend Stonebloc for homeowners as “it’ll make your home and landscape stand out and add value”. The retaining walls last generations, providing an everlasting solution.
Wanting to add value to your home? Get in touch to build Stonebloc retaining walls
Liveable Streets is a joint venture between HEB Construction and Higgins Contracting. Its primary goal is to deliver the Central East Road Corridor Maintenance Contract for Auckland Transport.
The Liveable Streets team is tasked with general maintenance, emergency management, renewals, rehabilitation, road rails, kerbs, crossing, and spill response.
Early in 2022 heavy rains resulted in landslides in Whitford, Auckland. Just 7m from the slippage site on Whitford Road, was housing. With further heavy rains expected, there was an immediate threat to property. There was also the added potential risk of damage to nearby power/utility lines which needed to be considered in the solution’s design. To keep the residents and community safe, a protection wall needed to be erected, fast.
Interbloc to the Rescue
Envirocon’s high productivity, quick reaction Interbloc Precast Concrete Wall System was chosen. When compared to the other options - timber and gabion baskets - it was a no brainer. Both legacy construction systems were too slow to install.
In contrast Interbloc allowed for rapid deployment, with trucks rolling in one after the other offloading blocks which were installed in real time. In just 4 days, 337 blocks were installed to build a wall 2.4m wide, 2.4m high, and 20.4m long.
Wall being installed by the TWC Contracting team
The wall will be in place for an uncertain amount of time and subject to high loads and hydrostatic pressures. Interbloc’s inherent flexibility added additional benefits. A unique block stacking configuration was required, eliminating the need for vertical reinforcing. This aided the speed of installation without compromising structural integrity. Interbloc mortarless interlocking system also allows for water to drain through the wall.
Another key benefit for Liveable Streets is the ability to non-destructively dismantle the wall with ease at any stage in the future and reuse the blocks for another structure or take advantage of Interbloc’s industry leading Buyback Guarantee.
Liveable Streets is an excellent example of the suitability of Interbloc for emergency slip management - a common problem faced by road maintenance contract holders across New Zealand. Similar solutions have been provided throughout the Waikato and Marlborough.
Interested to know more? Get in touch today.
The Morrison family is well-known in the Warkworth community, having owned land near the township for many years. In recent years Bevan Morrison has been converting the family land to industrial and commercial developments to support the town's rapid growth.
In April 2021, Bevan reached out to Envirocon looking for some blocks for his farm. Once Bevan heard about the unique Stonebloc block, he started to explore using it on his upcoming commercial development.
That development required a retaining wall to support a carpark. Council requirements also meant the wall needed to have street appeal and serve as a wheel stop - Stonebloc provided the ideal solution.
(Car parked behind the Stonebloc retaining wall that serves as a wheel stop)
Why Stonebloc was chosen
For his retaining wall, Bevan was looking for something that was “functional that also looks good”. He was also looking for something that was fast to install and could be done with a digger.
Stonebloc was chosen for a few reasons:
- The blocks are a larger square meterage compared to other modular retaining wall systems, meaning installation is faster
- The blocks are flexible with their facia design. If Bevan wants an exposed facia or oxide blocks for future projects, it can be done
- The blocks can be installed with a small digger
- “Looks more real than other options out there”
- “Support was really good and responsive”
Comparison to other retaining wall options
With commercial properties, an important aspect of retaining walls is longevity. After looking into alternative systems such as timber retaining walls and other concrete modular walls, Bevan chose to go with Stonebloc.
Although timber retaining walls came out slightly cheaper for his 800mm wall, Bevan wants to keep this property in the family for generations. For this, walls need to last and require little maintenance. Timber retaining walls after 20 years start to deteriorate, and you don’t get this with concrete. For Bevan, choosing Stonebloc at the beginning beats out the lower cost and repeated maintenance of timber retaining walls.
“Slight premium you pay over timber is well worth it to look good” - Bevan Morrison
One of the other reasons Bevan choose Stonebloc was the size of the blocks. Stonebloc allows commercial developers to install with a digger. The standard block size (800mm L, 400mm W, and 400mm H) are in between that of the competitors sizing. For the application of the car park, the Stonebloc sizing was the perfect fit.
Why Bevan Recommends Stonebloc
As a developer/business owner, Bevan chose Stonebloc as it will look good forever, giving him reassurance his investment is worthwhile. It means that as this property passes down the family, they don’t have to worry about maintaining the wall.
Bevan loves companies that are trying something new that has “local product and local people”. He’s definitely use it again and would recommend it for applications like this.
Stonebloc’s flexibility lends to creative design. There is no better example of this than the South Taranaki District Council’s (STDC) seawall at Opunake Beach.
Opunake Beach is a popular beach in the South Taranaki District. It’s a well-known spot for surfers, even being called “Home of the Big Wave”. Here, an existing crib seawall collapsed making it no longer fit for purpose. This caused risk to the community, creating a need for a durable replacement that can withstand erosion and rising sea levels. Jayson, the Projects Engineer at STDC describes the old seawall:
“ The previous lattice wall design was prone to disintegration brought about by sea water waves coming through. The structure was built in 1995.”
From what Jayson has stated, it is clear the new seawall needed to meet strict criteria - the main criteria being erosion protection.
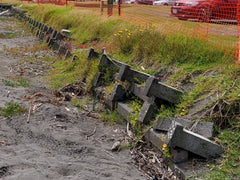
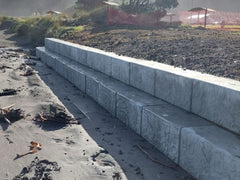
Stonebloc was chosen as it met STDC and the community’s needs. It ticked off a lot of the boxes, including:
- It can be built fast, reducing potential health and safety risks
- It can withstand the coastal environment
- It can be built over service outlets
- It looks good
- It provides “Quick installation and it's clean-looking aesthetic wise” - Jayson, STDC
Erosion protection was one of the most important aspects of this project. After years of coastal activity, extreme water levels played a large part in the collapse of the crib wall. Chan Zhi Han, Chartered Engineer from Resilient Structures found that backfill had been washed away during tidal/storm events which left the concrete elements of the crib wall unsupported. It was recommended the future seawall extend the drainage outlets seawards. This ensures the base will not be undermined, leading to a risk of local destablisation.
(Drainage pointing seawards for the Stonebloc wall)
Another important element considered was the design pressure. After calculating 8 different designs, Chan recommended a tiered Stonebloc seawall. This is because it provides reassurance of high-quality protection with the lowest amount of design pressure. Chan also noticed evidence of beach scraping which may have contributed to the original wall's damage. The likelihood of damage being made by mechanical equipment was considered with the Stonebloc design, along with the need for erosion protection.
(On the left is a standard Stonebloc block. On the right is one of the custom blocks that was used for this STDC project)
The result of creating custom blocks was a strong seawall with a functional seating area for beach-goers.
(A beach-goer sitting on the tiered seating of the Stonebloc Seawall)
With Stonebloc, you can make your designs come to life. Get in touch with us to start creating.
Ram raids have increased over the past few months across New Zealand. Many retailers, small business owners, and security companies are looking into loss prevention tactics to counteract the effects of ramraids. To help the community combat this, we introduced BollardBloc - a block that’s both a bollard and outdoor furniture.
Ram raids can have a dire effect on businesses, communities, and people alike. Nathan, the Loss Prevention Manager from The Briscoes Group states:
“Ram raids aren’t just about the loss of stock, it’s also about damage to the building and morale which takes a big dive in these sorts of situations, the cleanup costs, then its months and months of repair work and waiting for the product to repair what has been damaged”
To avoid these impacts from ram raids, The Briscoe Group reached out to us to install BollardBloc in a selection of their Rebel Sports and Briscoes stores. Prior to using our system, they used bollards that were embedded deep into the ground. Because of the services that ran underneath the paths, The Briscoes Group needed a solution that could sit on top.

( On the left, Nathan is placing BollardBloc next to their existing bollards)
Installation for BollardBloc is simple. Unlike traditional bollard systems, you just need to place BollardBloc where you need it. You don’t need to pull up any concrete or disrupt services to protect your property. In most cases, you also don’t need council approval to place BollardBloc.
The Briscoes Group chose to go with BollardBloc for a number of reasons. The main reasons being:
- It can sit on top of footpaths -There are services running under where they needed their bollards to be so traditional bollards were not an option.
- It’s strong - measuring between 1200 and 1800 milimetres and weighing from 1 tonne to 1.5 tonnes
- It functions as furniture - customers can have a place to sit if they need to
To understand the positive impact of having BollardBloc as ramraid protection, watch the video below with Nathan from The Briscoes Group.
Wanting a simple solution to tackle ramraids? Buy BollardBloc
Hamish from HP Works Ltd is an experienced Stonebloc Installer, and has recently completed a Stonebloc project in Campbell’s Bay.
Prior to Stonebloc being installed, this homeowner had timber retaining walls. Over time (it’s estimated this wall was built in the 1970s), this timber retaining wall failed, creating an urgent need for the customer’s retaining wall to be replaced.
Timber was out of the question. With its failure in the past, the customer was looking for a more durable option - one that could stand the test of time. Stonebloc was chosen due to its strength and high quality aesthetic.
The previous retaining wall created a terraced space - with a lower and upper section. To create something more usable, the customer decided to remove the terracing entirely, choosing to have just one supportive retaining wall across the boundary line.
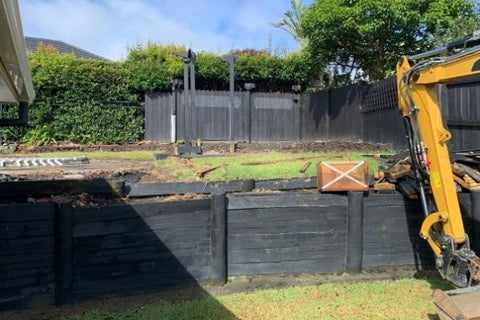
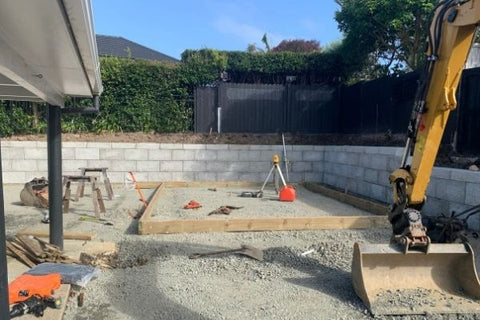
(Before this area had 2 levels. With this new retaining wall, the customer requested there to be no terracing so they had more usable space. Earthworks was completed, pushing the retaining wall to the edge of the boundary line)
Here's what Hamish had to say about this project:
"The use of Envirocon's Stonebloc range allowed me to build a solid low maintenance retaining wall that my clients and their neighbors approve of."
Wanting a Stonebloc wall similar to this? Get in touch!
B & T Earthmoving was contracted to make install a retaining wall on high-density development in Epsom, Auckland. This project came with difficulties that traditional retaining wall solutions would have difficulty adapting to. Stonebloc was easily able to work around these difficulties and offer a well-designed, presentable wall.
A prominent feature in this site was bedrock, meaning traditional poles and footings were not an option. For ground like this, retaining wall solutions need to sit upon as opposed to being dug into. Not only was bedrock an issue, but so was tight access. The retaining wall solution needed to have the ability to be built on the boundary line.
Both of these factors - bedrock and tight access - can be remedied by Stonebloc. The fact that Stonebloc could be installed quickly and could be laid on a bed of metal were the main reasons the contractors chose the product.
From the contractor’s perspective, installation is very simple and fast. Unlike their solutions such as masonry, there is no grouting or gluing. The blocks stack together much like LEGO.
Here what Phil from B & T Earthmovers had to say about the project
If you're needing a retaining wall solution that can adapt to tight sites and tough ground, look no further than Stonebloc.
“At Daltons we are the best in our field and we like to deal with the best and that’s why we chose Interbloc” - Kerryn, Auckland Area Manager
Daltons is one of New Zealand’s largest landscape supplies businesses. Their products range from fertiliser and compost to aggregate and mulch. Key to Dalton’s success has been their investment in state-of-the-art manufacturing systems and commitment to quality. Tidy, flexible, and efficient bulk materials storage plays a small, but important role as well. Since 2008, Daltons have chosen the Interbloc precast wall system to build their storage bins.
(Interbloc Bin for Daltons Landscape Supplies' Christchurch Yard)
One of the most common solutions that Daltons has used is Interbloc bins. A natural benefit of the bins is it separates their product, making it easier to pick out what’s needed. That’s not the only reason why they chose Interbloc, though. A key plus for them has been the flexibility in the system. Giving them the ability to grow (or shrink) their bins as needed.
“ We can change it. If our bins are too small, we can make them wider, it’s just putting in another footing, putting the rods back in, and restacking them” - Kerryn Gibson, Dalton Landscape Supplies Auckland Area Manager.
Daltons has used the Interbloc solution time and time again. So when it comes to designing or redesigning their yards, it’s easy. This is largely thanks to Interbloc’s intuitive and simple modular design. With the blocks’ interlocking shear key, it is quick and easy to build structures.
Cleanliness is also an important factor for landscape yards. Landscaping is all about creating a space where aesthetics are important. To fit this concept, storage solutions need to create a clean and organised environment. Interbloc fits the brief largely because of its modular design.
“The tidy aspect is something for a landscaped yard. You want to stand out and look good”
If you’re wanting a well-organized landscape yard that suits your current and future needs, get in touch:
https://www.envirocon.co.nz/pages/contact-us
We also offer other Interbloc solutions, some of which are:
Stonebloc is a gravity retaining wall system that’s designed for contractors to provide fast installation with minimal labour. The result is a system that delivers the speed and durability of precast concrete, for less money.
Phil of B&T Earthmoving used Stonebloc for the first time at a challenging site in Auckland. “It was a really rocky site, as well as tricky and tight,” he explained. Despite it being the first time the company had used Stonebloc, they soon found it was a lot easier to set up and a lot quicker to install than anything they’d used before.
They found that good preparation was key to delivering a good looking and long lasting wall. While no grouting or gluing was needed between the blocks, making it a lot easier and quicker to construct, initial site preparation was really important. The ground had to be levelled correctly before the first blocks were laid, but once that was sorted “set up was easier and a lot quicker,” he said.
He feels the interlocking blocks with their decorative fascia look really good. Stonebloc walls can be built right up to the boundary, which maximises the usable area for homeowners – something that’s increasingly important in today’s smaller lot sizes. Stonebloc’s solid, upcycled concrete blocks offer a unique interlocking design that provides shear strength in both horizontal directions.
Neville is a site foreman at ICB, and his team used Stonebloc for the first time on a big project that required 729 lineal metres of retaining walls. He also found that good base preparation was the key to a quick and easy install – easier than other stone walls to install, too.
“It’s like a big kids’ LEGO set,” he said. Using vertical weight [gravity] maximises stability, which means Stonebloc retaining blocks lock together easily - and stay together.
“You have to get the bottom blocks right first, and they have to sit properly. Then you can work your way through, and up, as you go. It’s easy, but you have to take time to make sure everything’s at the correct angle.” This allows the wall to take the loadings and remain stable and straight, especially on a sloping site.
This project used Stonebloc’s newest product - double-ended blocks - as well as ones specially-manufactured for this job that allowed for specific angles at site boundaries.
Stoneblocs are made from solid concrete, and in wet weather any building site becomes really muddy. They found that storing the pallets of blocks close to where they were installing them, saved a lot of time and energy.
The finished project was something the whole team was proud of. The ICB team includes:
- Arnulfo Nartea - Forman & Digger Operator
- Joey Gurrea - Skilled Digger Operator
- Adam Suaesi - Skilled Labourer & Digger Operator
- Teremai DIxon - Skilled Labourer & Digger Operator
- Anaru Morris - Forman & Digger Operator
- Chris Endt - Skilled Labourer & Digger Operator
- Perry Carr -Skilled Labourer & Digger Operator
(Some of the ICB Team who built Stonebloc walls in Auckland)
The Stonebloc retaining wall system is proven to withstand significant loadings – it’s been independently tested by the University of Auckland School of Engineering. Stonebloc’s consent-ready designs use conventional engineering principles and cover walls 0-12kPa and up to 2m high.
Want to find out more? Read our 9 Top Tips for Installing Stonebloc.
Contact us now to find out how you can work smarter with Stonebloc on your next retaining job. It’s a timeless solution the client will love as much as you do.
Fulton Hogan is one of New Zealand’s leading civil contractors. They have a deep commitment to building the infrastructure that powers economic growth. Most recently, this has meant they’ve expanded asphalt production at their Silverdale plant in the rapidly expanding area of North Auckland. Key to asphalt production is aggregate storage. Envirocon’s Interbloc wall system was used to build flexible, durable, and safe storage bunkers.
When additional aggregate storage was required at Fulton Hogan’s asphalt manufacturing plant in Silverdale, the company specified Interbloc. It was a no-brainer - Fulton Hogan has extensive experience utilising the Interbloc system throughout the country for similar purposes.
12 bins of varying sizes were constructed from the Interbloc precast wall system, giving an additional capacity of 1,750m3 of aggregate storage, equal to 2,750 tonnes of material.
To complicate matters, the bins had to be built at the top of a 3m high retaining wall on three sides. The combined weight of the filled bins and the backfill material meant that engineers needed to be satisfied that the retaining walls would be able to handle such loads, especially since unsuitable base soil meant retaining walls had failed in the past. Interbloc showed its unique versatility by allowing high surcharge capacity reinforced earth walls to be built by simply casting geogrid into the blocks during the manufacturing process.
“Due to the steep topography of the landscape, a retaining wall was constructed out of Interblocs to provide a level surface for the aggregate bins to be built on,” explained Fulton Hogan's Project Engineer Oli Brooks. “Geogrid was used in the backfill behind the retaining wall, and tied into the blocks. Granular backfill (DQ65 which has a compacted dry density of 2.14tonnes/m3 ) was then placed and compacted in 150-200mm layers, with geogrid installed at each Interbloc row ", explains Envirocon’s Peter Fowler.
The asphalt plant had to remain in production throughout the expansion process. As a result, the 20-year-old storage yard had to be deconstructed in stages. This meant temporary bins were built using Interblocs, in a different area of the yard, to accommodate some of the material while the full operation of the plant continued. These blocks were then re-used at the final bin sites.
This project was the first to use the new Interbloc base block for the storage bins. The combined forces of the product, the height required to store materials in the footprint available - and to provide support for a fixed roof – meant base blocks could spread the wall load over a bigger footprint, delivering greater design efficiency.
(Holding the aggregate bins (with the new Interbloc Base Block) up is a 3m long retaining wall)
All bins were assembled on-site, and Brooks felt the process was “pretty straightforward - the 3D drawings helped significantly,” he said. This was critical as the density of stored aggregates varied between 1.4 to 2.3 tonnes/m3.
“The new layout and storage volumes have removed the safety and storage problems, and future-proofed it for many years to come,” said Peter Fowler proudly.
The Interbloc system easily absorbed the loadings required of such a structure, and the team found its construction very straightforward.
The number of 3D drawings of the block layouts supplied by Envirocon really helped the team visualise what they were building, said Brooks. “This made the whole process go a lot more smoothly.”
Brooks particularly praised the support received from Envirocon during the build. “The Interbloc team, specifically Peter and Cole, have been very responsive and accommodating to design changes and last-minute requests,” said Brooks. “And the 3D drawings of the block layouts were very helpful for the site team to visualise what they were building.”
Williams Corporation has a reputation for developing high quality, affordable homes throughout Auckland, Wellington, and Christchurch. In ten years of operations, Christchurch based Williams Corporation has grown to be one of NZ’s largest residential developers.
The secret to their success is the ability to maximise land utilisation, focusing on high density infill housing. Stonebloc has proven to be an excellent retaining wall system to accommodate this type of building. Stonebloc walls can be built vertically on the boundary and deliver unparalleled durability at a price point similar to timber walls.
When Williams Corporation developed nine dwellings on an 800sqm site at St Leonards Road, Kelston, Auckland their long term civil contractors DiggersNZ were able to install the walls. DiggersNZ is a national company specialising in foundation excavations, site cuts, backfills, trenching and more. Doing away with the need to bring in specialists retaining wall contractors, Stonebloc provided Diggers NZ with the flexibility to progressively build walls as required.
Mike Hawke is DiggersNZ Project Site Manager and like Williams Corporation, he’s a fan of the Stonebloc system. “We’re familiar with the principles involved with assembling Stonebloc,” he said. The solid concrete blocks can be stacked easily and need neither glues nor grouts to hold them in place, meaning a standalone gravity wall can be constructed very quickly – saving assembly time and maximising value for money.
Each Stonebloc is 400mm thick solid concrete, and similar to well-engineered LEGO it uses a unique design and interlocking shear key for an exceptionally robust wall. The textured fascia of Stonebloc comes in a range of patterns, providing visual interest and positive placemaking for both residents and visitors.
“Stonebloc is a win-win system”, explains Jack Bright from Envirocon. “It’s a win for developers as it delivers a superior wall system at, or close to, a timber price point. It’s a win for council’s as it delivers a resilient structure that can be non-destructively dismantled in the future for maintenance or access to utilities. It's a win for civil contractors as it's a locally manufactured, high productivity system.”